100% uptime with your switchgear? Impossible dream … or a new reality?
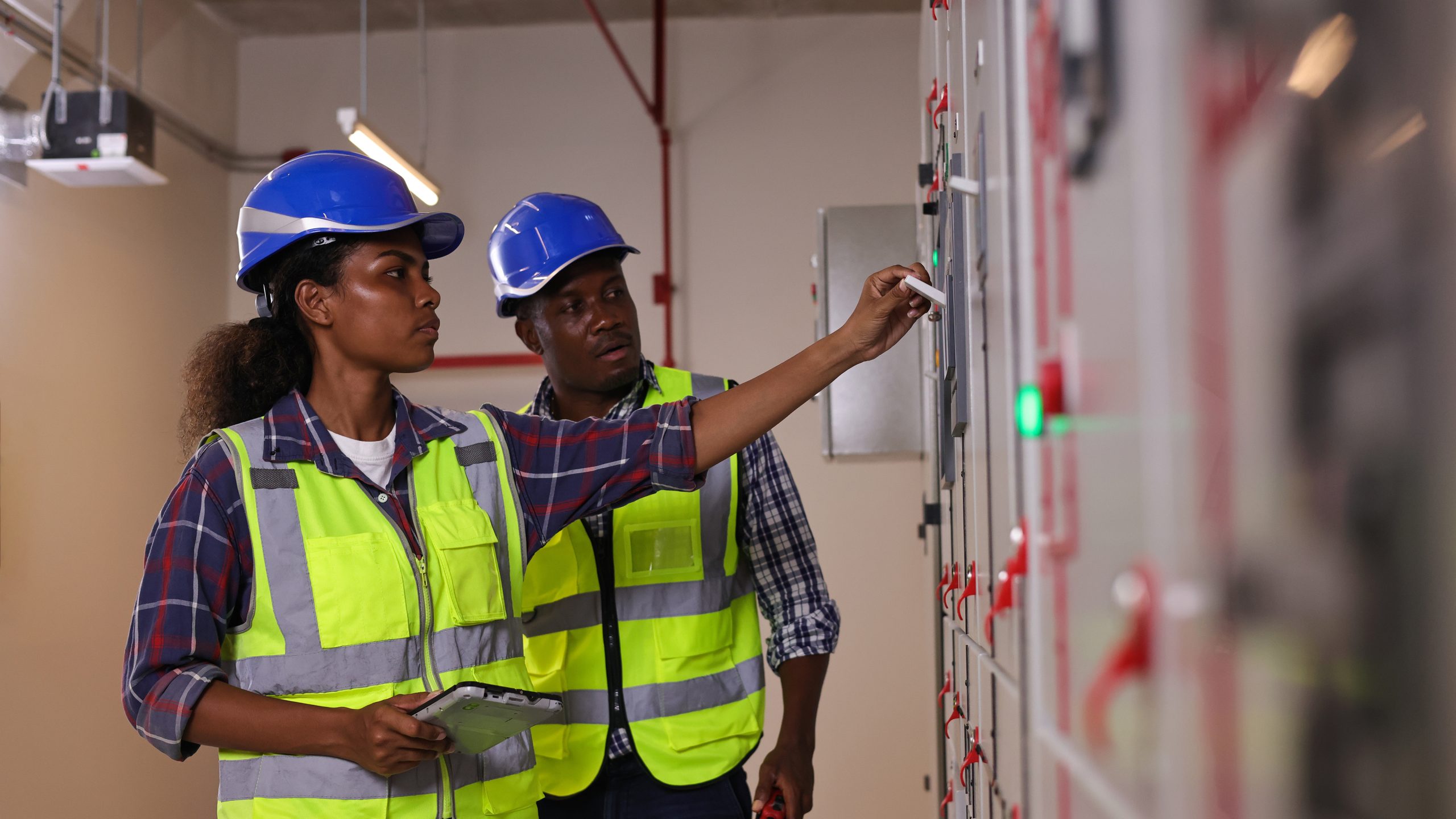
Engineering managers in South Africa have their work cut out for them when it comes to achieving 100% uptime for their MV switchgear. They face a daunting task with an infrastructure that has to withstand unreliable and frequent power outages that play havoc with critical systems. Most MV switchgear systems are designed for long or continuous operation and not for the on /off situation caused by loadshedding. However, various technologies are available to ensure that switchgear remains operational – from remote monitoring to predictive maintenance and backup systems. These tools can become a formidable arsenal to help to keep systems running smoothly, even in the most adverse conditions.
Remote monitoring is one of the most critical technologies for achieving 100% uptime with switchgear. With remote monitoring, you can keep a close eye on systems at all times, allowing quick detection of any issues that arise and taking corrective action before they become serious problems. Remote monitoring can be especially beneficial for plants in remote or hard-to-reach areas.
The power of remote monitoring
Remote switchgear monitoring typically involves sensors, data analysers, IOT monitoring devices and software for realtime data collection and analysis. This technology enables monitoring of critical parameters such as temperature, current, and voltage. More often these days – online partial discharge monitoring of busbar, breakers, cable terminations and cables and receiving alerts when these readings exceed predefined thresholds. In addition, remote monitoring solutions often include advanced analytics capabilities, such as machine learning algorithms, that can detect patterns and anomalies in the data that may indicate potential issues. Leveraging these technologies can proactively identify and address problems before they cause downtime or operational disruption.
A multi-sensory approach
Switchgear can be equipped with various types of sensors to monitor different aspects of its performance. For instance, temperature sensors can detect overheating in circuit breakers, transformers, or other components, indicating potential failures or other issues. Current sensors can measure the electrical current flowing through different switchgear parts, providing valuable energy consumption and performance data. Voltage sensors can monitor the voltage levels at various points in the system, helping to identify any irregularities that could lead to malfunctions or damage. Other types of sensors used in switchgear include partial discharge gas pressure (SF6), humidity, and gas sensors, which can detect leaks or other abnormalities that could pose safety risks to staff or compromise the reliability of the equipment.
Typical switchgear failures and the technologies used to prevent them
- Partial discharge / Arcing and tracking: Cause significant damage to switchgear components and increase the fire risk and safety to staff in the substation environment. Technologies used: ultrasonic monitoring, infrared thermography, partial discharge analysis/monitoring.
- Contacts erosion: Contacts in switchgear can wear out over time, leading to increased resistance and decreased performance. Technologies used: partial discharge monitoring, ultrasonic monitoring, resistance monitoring.
- Insulation breakdown: Insulation breakdown can cause damage to switchgear components and increase the risk of electrical faults. Technologies used: partial discharge monitoring, insulation resistance monitoring, ultrasonic monitoring, thermal imaging.
- Corrosion: Causes damage to switchgear components and increases the risk of electrical faults. Technologies used: ultrasonic monitoring, visual inspection, electrochemical impedance spectroscopy (EIS), and corrosion monitoring sensors.
- Mechanical failures: Occur on switchgear components leading to reduced performance and increased downtime. Mechanical failures can be prevented by monitoring the condition of switchgear components, detecting issues early on, and performing maintenance to extend the life of switchgear components.
A comprehensive view of the switchgear’s condition is obtained using these tools and technologies, and predictive maintenance comes to the fore. Thus, we can prevent failures before they occur with proactive steps to optimise performance, minimise downtime, improve equipment reliability and minimise the risks associated with equipment failure.
Predictive maintenance strategies
In addition to these technologies, several other strategies come into play to achieve that elusive 100% uptime with switchgear. For example, one can implement redundancy and backup systems to ensure critical systems remain operational even if one component fails. Comprehensive testing and training programmes can be implemented to ensure staff can quickly and effectively respond to any issues. For example, we consider what risks condition monitoring can avert in a power plant.
What risks can remote monitoring avert at a power plant?
Condition monitoring is critical for ensuring safe and reliable switchgear operation at a power plant. For example, temperature sensors can detect hot spots in the switchgear that could lead to equipment damage or fire. By detecting these hot spots early on, one can implement measures such as cooling or rerouting the circuits to prevent further damage. Similarly, PD scanners, ultrasound, or vibration sensors can detect abnormal vibrations on external parts of the switchgear. These vibrations may indicate loose connections or faulty components, which could lead to arcing or other electrical faults. By addressing these issues promptly, the risk of electrical faults, outages, and other disruptions that could compromise the safety and reliability of the power plant is reduced. Overall, condition monitoring ensures smooth and safe switchgear operation at a power plant.
Do you have a significant edge over your competition?
In today’s fast-paced and highly competitive business landscape, achieving 100% uptime with switchgear is no longer a luxury but a necessity. Adopting a comprehensive approach incorporating cutting-edge technologies, practical strategies, and best practices ensures that your critical systems remain operational and reliable. Whether you’re operating in the mining, manufacturing, or energy sectors, leveraging the latest tools and techniques can give you a significant edge over the competition and help you stay ahead of the curve in this rapidly evolving industry. With the right approach, achieving 100% uptime with switchgear is not only possible but essential for the success and sustainability of your operations.
While achieving 100% uptime with switchgear is critical, it is only one part of ensuring critical systems’ safe and reliable operation. Another vital component is transformer technologies, which are crucial in maintaining stable and efficient power delivery to critical loads.
In our next article, we will unpack the current transformer technologies and explore how they can be leveraged to achieve 100% uptime. From smart transformers to predictive maintenance tools, we will examine the latest trends and best practices in transformer technology and offer insights on staying ahead of the curve in this ever-changing field.