Avoid extended downtime due to inadequate preparation prior to start-up after lockdown
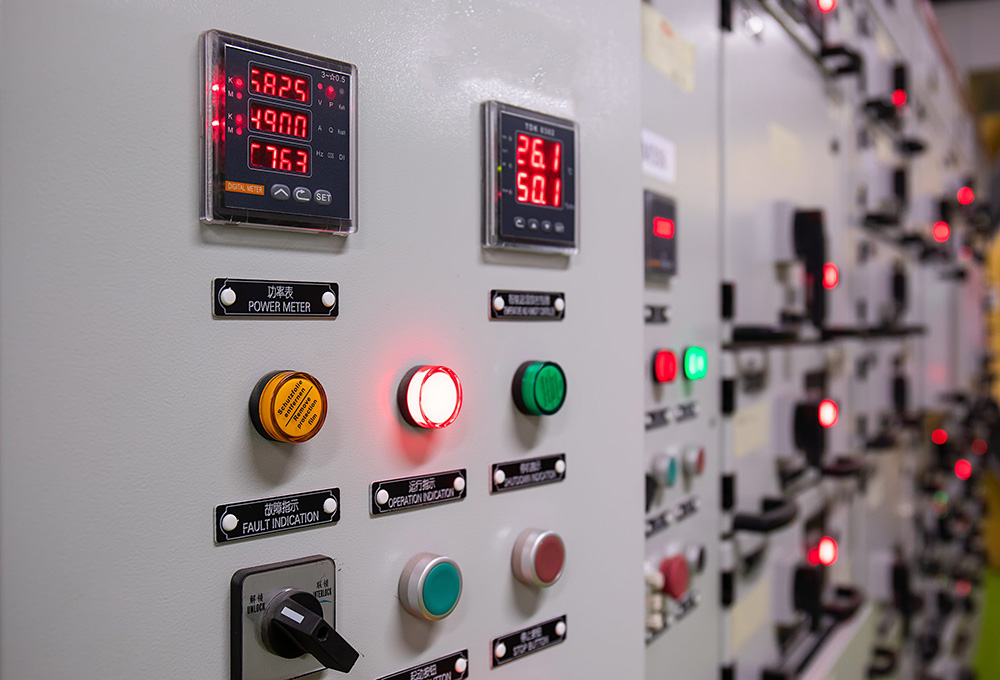
Evaluate the risk the shutdown posed to Critical Electrical Equipment (CEE) before you start up your plant after lockdown.
During normal circumstances, a plant shutdown is a thoroughly planned event where several processes are precisely orchestrated to take equipment out of service, maintained and then meticulously returned to service. This process is usually conducted by highly experienced engineers who understand the hazards posed to equipment, people and the environment. Specialised tools, such as condition assessment and monitoring equipment, are crucial to these engineers’ toolsets.
In exceptional cases, like the Covid-19 lockdown, some industries had to hastily shut down without the normal time required to plan and execute shutdown processes properly.
Where the necessary shut or preservation scope was neglected for motors, cables, transformers and switchgear, which are the most commonly used electrical assets in industrial plants, a prolonged period of inactivity could deteriorate and harm several components and impact on the reliability and safety thereof.
Failing to follow the required inspections and testing processes prior to re-energising equipment may result in extremely hazardous conditions that cause severe damage to the equipment, extended plant downtime or could even lead to fatal flashovers.
Unpacking the risk and mitigation
One of the most common electrical failure modes is a flashover due to compromised insulation. Thus the early detection and identification of deteriorating insulation is a key predictive maintenance tool to address this problem. The different stresses that increase the rate of insulation degradation can be summarised into the TEAM Stresses:
Thermal | High thermal stress during the start-up process deteriorate insulation systems until failure
Electrical | Poor electrical installations are the number one cause of failure
Ambient | High operating temperatures and moisture ingress contribute to failures
Mechanical | Poor electrical contacts can add to premature failures
Performing routine commissioning or pre-energisation assessments are imperative, and techniques such as insulation resistance, polarisation index and oil analysis are some of the more well-known assessments. During energisation, the best method to determine the impact of TEAM Stresses is with on-line partial discharge technologies.
Following are examples of the typical risk conditions encountered after prolonged periods of inactivity on High Voltage (HV) and Medium Voltage (MV) equipment, and specific condition monitoring techniques that can be used to identify these conditions.
Medium Voltage Switchgear
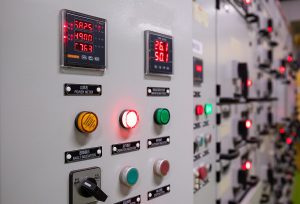
MV switchgear that is used in hostile environments can be exposed to various corrosive contaminants, which damage both the insulation system and metal components (including the internal components of breakers). During out-of-service conditions, they tend to gather dirt, moisture, contaminants and even vermin, which can lead to flashovers and protection failure.
Visual inspections and condition assessment using handheld or advanced on-line technologies should be conducted after racking the breaker into position, just before switching activities to resume.
Once the incomer switchgear breakers are returned to service and no electrical anomalies are identified, the rest of the switchgear breakers can be returned to service by gradually stepping up the load to full normal load. This reduces the risk of simultaneous large loading within the power circuit and high starting currents, voltage dips and protection trips or failure (arc flash).
Transformers
Oil-filled transformers are commonly used in plants, and their oil provides an insulation medium as well as cools the transformer. These transformers have sealing systems to prevent the oil inside the transformer from coming into contact with air and moisture that contaminates the oil and cellulose insulation and ultimately deteriorates the insulation properties. Moisture generally enters through leaking gaskets, cracks or seals, accelerating the deterioration of insulation. This results in 90% of all preventable bushing failures, reduces the useful life of the transformer and can lead to explosive failures, causing extensive damage to the transformer, surrounding equipment and buildings as well as endanger people’s lives.
During prolonged periods of inactivity (or long periods of not being energised) the transformer cools down, allowing the moisture that is otherwise suspended in the oil to condensate from the oil and compromise the insulation system.
Visual inspections should be conducted to check for rust, leaking gaskets, seals, cracks, correct oil levels and to evaluate the colour of the silica gel. Oil samples should be taken and analysed if leaks are identified during the visual inspections. Based on the results, the needed corrective action should be planned that could range from drying the oil to more advanced repairs.
While returning the plant to service, loading on the transformers must be gradually stepped in, to reduce the probability of failure caused by higher moisture content at low temperatures. This failure frequently appears post shut periods where loads are not stepped in.
Detailed oil analysis forms the cornerstone of managing reliability on oil-filled transformers and could be complemented with technologies such as ultrasound and thermography in monitoring bushings and cooling systems. It is advisable to implement an in-time monitoring solution for Dissolved Gas Analysis (DGA) on critical and/or ageing oil-filled transformers in order to trend the health and prevent premature failures that could be missed by normal oil sample frequencies.
MV and HV Motors
Motors are the most common electrical assets used in industrial plants and mining operations, and they often play an essential role. If a critical motor fails, it can result in a variety of safety hazards and costly downtime. Motors often fail during start-up, so they must be in a good state before they are brought back into service. The most prevalent failure mode on motors is bearing-related and can include worn bearings, bearing housings or shafts. Contamination can also cause binding. Before energising motors, the best practice is to check all lubrication systems and oil levels to ensure that they comply with desired standards.
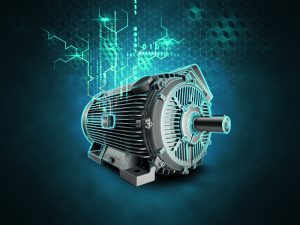
At this year’s SPS IPC Drives, Siemens is demonstrating the connectivity of Simotics IQ, the new IoT concept for Simotics motors.
Secondly, a minimum requirement is the verification of the winding insulation integrity on MV and HV motors by performing a polarisation index test.
Thirdly a visual inspection of power cables and terminations are done to ensure that the correct connection criteria are applied, and no insulation damage is visible. Cable theft is a problem in some areas, in particular when the cable is not energised or the plant is relatively quiet in terms of employees moving about.
If an MV motor can’t be tested off-line (polarisation index test), an on-line assessment with advanced condition monitoring technologies (i.e. partial discharge) is recommended during energisation. Engineers use the data derived from the advanced on-line assessments on the cables, terminations and winding insulation systems to determine the MV motor insulation health.
A motor’s lifespan can further be extended with the integrated use of condition monitoring technologies such as vibration, ultrasound and thermography. A holistic view of the motor’s condition (cooling system, bearing hot spots, etc.) can help detect several problems before they start to create serious damage. It is a worthwhile investment to consider.
MV and HV cables
Cables that cool down due to the full termination of energy, or reduced current capacity, tend to attract moisture through any small imperfections within the outer insulation system. This is more likely to occur with PILC cables that uses paper as main insulation compound and sometimes even XPLE cables.
During start-up, the inrush currents drawn by the equipment connected to the cable can cause underlying defects to result in a complete cable failure and pose a significant safety hazard that will most probably result in prolonged downtime.
It is strongly recommended that a number of tests are conducted to ensure that cables are intact before commencing with re-energisation. A VLF test (using SANS 10198-13_2016) is performed on critical incomer feeder cables prior to re-energisation to ensure that the cable is electrically sound and that no sections are missing due to theft. VLF (pass/fail test), Tan Delta and Partial Discharge assessments are done to confirm, amongst other, the quality of electrical insulation, the degree of deterioration of shielded cable insulation caused by contamination, damage or water tree and the possibility of a flashover. Used complementary to each other, it is possible to determine the overall health and condition of critical cables before resuming service safely.
During downtime, higher moisture content may be present in cables due to lower temperatures and can potentially result in failures once re-energised. When returning the plant to service, electrical loading on the cable must be ramped up in phases over an extended period to validate system behaviour. This is known as “soaking” the cable or soak testing. On-line condition assessment with advanced technologies can also be used to verify any partial discharge activities within the accessories and feeder cables to detect and prevent potential failures.
What to do? Checks and assessments
During the shut period, several best practices must be adopted on MV/HV electrical equipment, such as:
- Keep motor space heaters on to prevent adverse moist conditions affecting the winding condition.
- Rotating machines with heavy shafts must be rotated periodically to prevent shaft bow. Put measures in place to prevent bearing corrosion.
- Keep switchgear energised with humidity and temperature monitoring.
- Inspect transformer breathers, with a specific focus on the silica gel colour, as moisture ingress may result in catastrophic failure (during shut and before start-up).
- Introduce measures to prevent vermin and contamination entering equipment.
Before commencing the return of equipment to service, the following pre-start-up checks and assessments are required:
- Inspect cable joints and terminations for moisture ingress, insulation deterioration and confirm the correct torque settings on connections (where applicable).
- Verify that the earthing system is still intact (in particular as the copper is prone to theft in some areas).
- Perform off-line VLF, Tan Delta and Partial Discharge (PD) assessments on critical electrical infrastructure.
- Inspect transformer breathers, with a specific focus on the silica gel colour, as moisture ingress may result in catastrophic failure
During start-up the following is important:
- It is important to have a well-documented sequential step by step start-up procedure that will mitigate the risks posed
- The energisation of the installed electrical plant should be gradually stepped up to full normal load
- Perform on-line PD assessments once the start-up process has commenced ensuring correct operation.
Although industries are now pressed for time and eager to return their operations to full service, it is advisable to carefully consider and apply mentioned best practices to ensure the reliable and safe commissioning of equipment. It is further recommended to partner with experts that can develop a full return-to-service scope based on your plant’s specific risks and that can perform the identified assessments and preventative tasks under quality-controlled processes.
It is recommended to partner with an expert that can develop a full return-to-service scope based on your plant’s specific risks and that can perform the identified assessments and preventative tasks under quality-controlled processes.
For more information, please contact Martec at info@martec.co.za.