Future of substation monitoring: It is not just the software
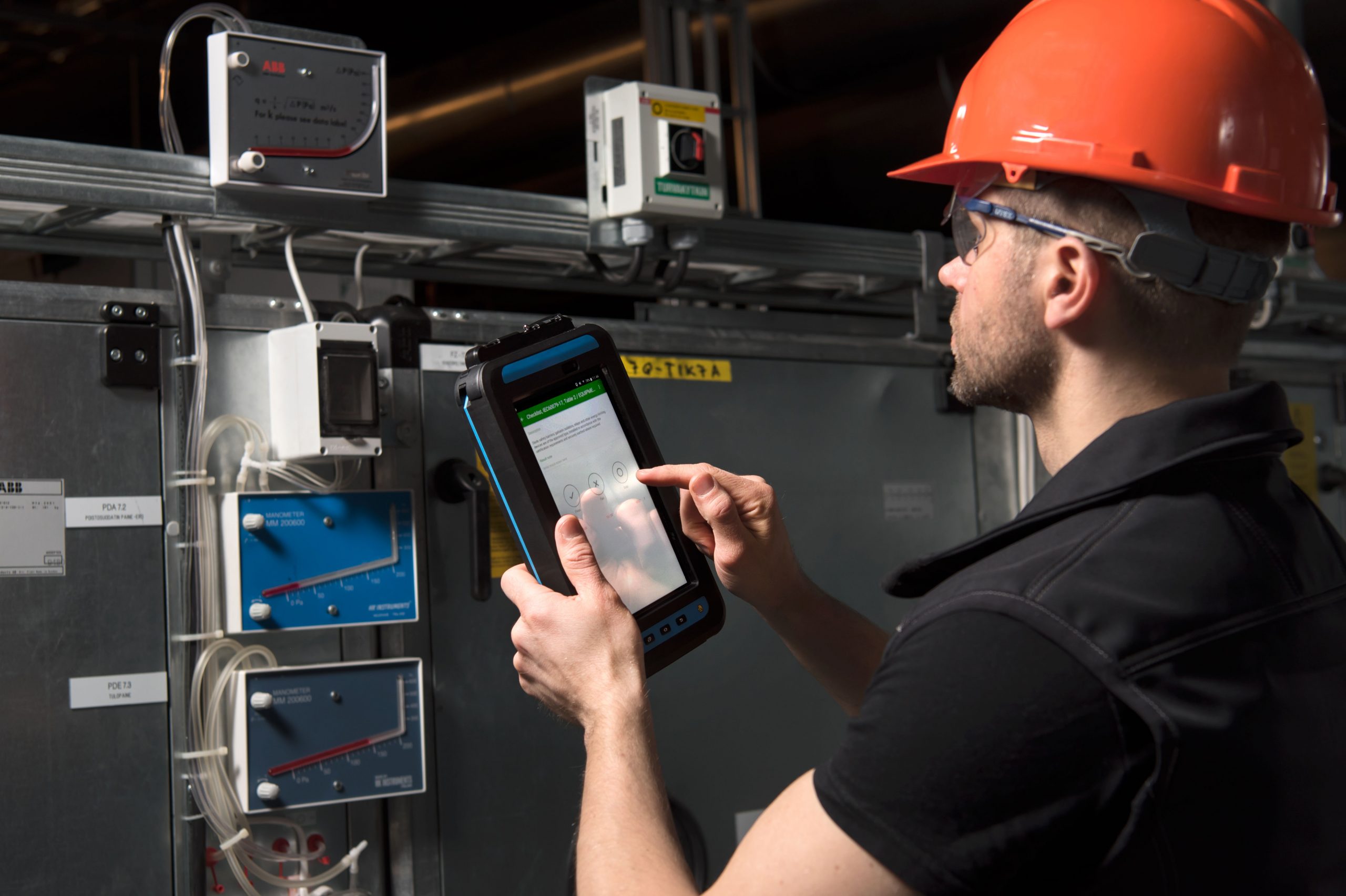
Brian D. Sparling, Senior Member of IEEE, and Regional Manager with Dynamic Ratings Inc.
The future of online monitoring of high voltage substation equipment is closely linked to enterprise asset management systems provided that proper measures are implemented for the EAM system to deliver the expected results. Those measures include trained personnel, detailed knowledge of one’s assets, technically and economically feasible maintenance process, the flow of information to personnel, and collaboration with a company that can provide the monitoring system as well as the expertise in its implementation. Monitoring and diagnostics are now part of the business process which contributes to a reduction in forced outages and a more secure and reliable system.
Introduction
I am an avid follower of various LinkedIn groups and have recently read with interest items from two diverse and separate groups, which, on the surface, appeared to have no connection with each other. One was from the Transformer Condition Monitoring group, asking the question “Is there a future for transformer monitoring and why/why not?”. I would refer the questioner to review my article published a year ago in Transformers Magazine for some of the answers.
Another item from the IAM Discussion group highlighted the author’s enterprise asset management predictions for 2018. I did touch on this topic of asset management in my previous article, yet found that this item provided more focus on why many of the systems fail to deliver on what the asset owner thought they had signed up for. In my mind, these two are connected. The future of substation monitoring is closely linked to the latest in buzz words or phrases such as Internet of Things (IoT ) and EAM. Full disclosure: I work for a company that engineers, produces, and provides engineering services to those companies owning and operating HV assets on the power system. We also produce asset analytics for those very same assets monitored.
Terrence O’Hanlon, CEO at Reliabilityweb.com, has noted what his company sees daily, not necessarily with electrical energy companies, but their observations carry over:
- a reminder that 80 % of the people who care about EAM and read this cannot access their work orders on a mobile device,
- only 40 % of the organisations they studied have an actionable EAM based asset registry,
- only 30 % of the organisations they studied have accurate and up to date asset criticality rankings.
Mr. O’Hanlon in his post predicts the following:
- Without an engaged and empowered workforce, EAM will still fail to create a positive return on investment.
- Without knowing what assets, you have, EAM will still fail to create a positive return on investment.
- Without a technically and economically feasible maintenance process (such as CBM), EAM will still fail to create a positive return on investment – no matter how much IoT you implement.
- Without adequate and ongoing EAM training, EAM will still fail to create a positive return on investment.
- Without active executive sponsorship, EAM will still fail to create a positive return on investment.
I will add another prediction: A failure to communicate – unique to utilities with remote substations, some located in geographically difficult to reach areas, either in terms of distance (hundreds of kilometers away from operational centres), or in times of extreme or even normal weather conditions (winter), which makes getting to the sites at times hazardous. Many who buy and install monitoring systems have not implemented the items necessary to take advantage of the data and information available for an EAM system. This can lead them to failure to create a positive return on investment (ROI).
Communications
Communication is extremely important and is a requirement that must be included in the scope of the plan. Without a means of notifying those who need to know (maintenance, operations, etc.) there is no point to installing a monitor, and just to allow it to be an ‘island of information’. Those who have been successful and have had proven ROI have engineered their ‘systems’ to include the pathway for all this non-operational data/information and alarms through a parallel communication channel, separate from the SCADA (or operational data) path. They may both use the same ‘pipe’ to transport the data, but each is secure from one another. Once back in a secure data historian with supporting applications, including the EAM, access to the information can be provided to maintenance personnel to carry out CBM activities, to operations personnel to have an awareness of the operating status, and to asset management personnel to develop their asset replacement strategies. Examples of this ‘failure to communicate’ include a bushing failing and taking the transformer with it, all due to the failure of the personnel to connect the alarm relays on the monitor to SCADA, RTU or annunciators. The operators had no indication of a failure condition in progress until it was too late.
What to do?
These observations can be used as a benchmark for HV equipment owners to act on. There may be logical and/or regulatory reasons why some of these items cannot become mobile, but technically speaking, there are no large hurdles. It is a process. Defining the problems and issues is the first step that can be answered by these five questions:
Why?
Why do we want to start online monitoring? Define in words why you want to move in this direction. Many of the common reasons are:
- Reducing the risk of unexpected failures
- Moving to condition-based maintenance from time-based maintenance
- Safety for workers and the public
- Less driving to remote sites, and sending the right team to the site
- Situational awareness of a unit’s condition before entering near the unit
- Extending the remaining useful life of units in service
- Capital deferment, cost savings on buying new equipment
Who?
Who will benefit from such a program? Define who and obtain their support for this move.
Who are the stakeholders:
- Maintenance groups – early warning of incipient defects
- Operations groups – situational awareness, how much load can this unit sustain, and for how long?
- Assessment management – understanding ‘risky’ units, plan for replacement
- Standards – writing specifications for new units, based on experiences of units in service
What?
What to monitor depends a great deal on the answer to the first question of “Why”. Some examples as identified through Failure Modes and Effects Analysis (FMEA) are:
- A vintage of bushings or on-load tap-changer (make, type), have over time had an increasing failure rate due to many reasons, aged gaskets, latent design/manufacturing defects.
- Defective ancillary devices, such as OTI and/or WTIs, have degraded over time and are no longer working/or out of calibration.
- Older units may be experiencing increased loading over time. The question becomes: can we keep increasing the load safely or is it time to plan a replacement?
Where?
Where to monitor depends a great deal on the answer to the questions of “Why” and “Who”, as well as input from operations load dispatch and asset management.
Some examples include:
- Critical loads served, government buildings, hospitals, heavy use of industrial loads (continuous processes);
- Increasing maintenance usually indicates units with either acute or critical deficiencies, and need extra intensive attention, before replacement.
- Generating facilities, with few or no spares, to replace units that unexpectedly fail. Lack of Generator Step-up (GSU) transformer = no revenue!
Who?
Who is going to be the champion or the ‘owner’ of the team and overall monitoring systems?
- This is a very important position and one that deserves a full-time commitment, not only to build the system but to have the support of the management to build the resources necessary for it to be a success!
- Without a passionate owner or champion of the dedicated team, it is doomed to failure.
The answers to these questions often overlook some critical and necessary elements such as training of personnel.
Training of personnel
Learning from others’ experiences, both good and bad, teaches us a lot about this new and modern approach to monitoring fleets of high voltage substation equipment.
Training needs to include not only the technology and its benefits but also training for operators and maintenance personnel on the new systems and the data/information available. There will be new sets of alarms that they have never encountered before, and many may not know how to respond. Developing an updated alarm response procedure is necessary to provide understanding to critical situations. The concept is to present the alarm(s) condition, transfer knowledge about the nature of the alarm, inform the reader what the consequences of ignoring the alarms may be, and provide recommendations to assist in decision making.
Who can help me? This is all rather new to me.
It is very important for the asset owner to work with a company that has demonstrated with other assets owners their capability not only to supply the ‘boxes’ that may be installed on the equipment but also have the expertise to understand the issues that will be unique to each situation (and substation), where this program needs to be implemented.
This company needs to be able to handle, from a project management point of view, all the requirements and inputs from operations, maintenance, asset management, and the IT departments, as well as the communications systems involved. Not all suppliers of the ‘boxes’ and/or EAM systems have that capability, nor domain knowledge of substation assets, to understand the unique applications involved.
In other words, ensuring measurements made on a piece of equipment are translated into actionable information, and delivered in a meaningful way to those who can then act on it, can be obtained by working with a proven supplier of not just a series of boxes and widgets, but one that has demonstrated that they can provide the systems you want, interfaced the way they want, that will seamlessly present the data where you want it.
Monitoring and diagnostics is now part of the business process
Those utilities that have demonstrated that this process provides a tangible benefit to their business understand that this is now becoming a key part of the other business processes any energy company has, such as HR, finance, and operations, to name a few.
It is one of the core competencies of their company that contributes not only to the bottom line, but also to an increased awareness of the worker and public safety, reduction in forced outages, and a more secure and reliable system which enhances customer satisfaction.
The EAM software developed for HV substation assets will deliver the expected benefits, provided the business owners provide the resources, both financial and structural, including a team dedicated to making it work, and has the plan to make it happen.
Bibliography
- B. Sparling, Online monitoring of HV substation assets: Myths and truths, Transformers Magazine, Volume 4, Issue 2, April 2017
- Terrence O’Hanlon, Top 5 Enterprise Asset Management (EAM) Predictions 2018, https://www.linkedin.com/pulse/top-5-enterprise-asset-managementeam-predictions-2018-ohanlon/ current January 4, 2018
This article was first published on Transformers Magazine Vol. 5 Issues 2