On-line monitoring of HV substation equipment: Myths and truths
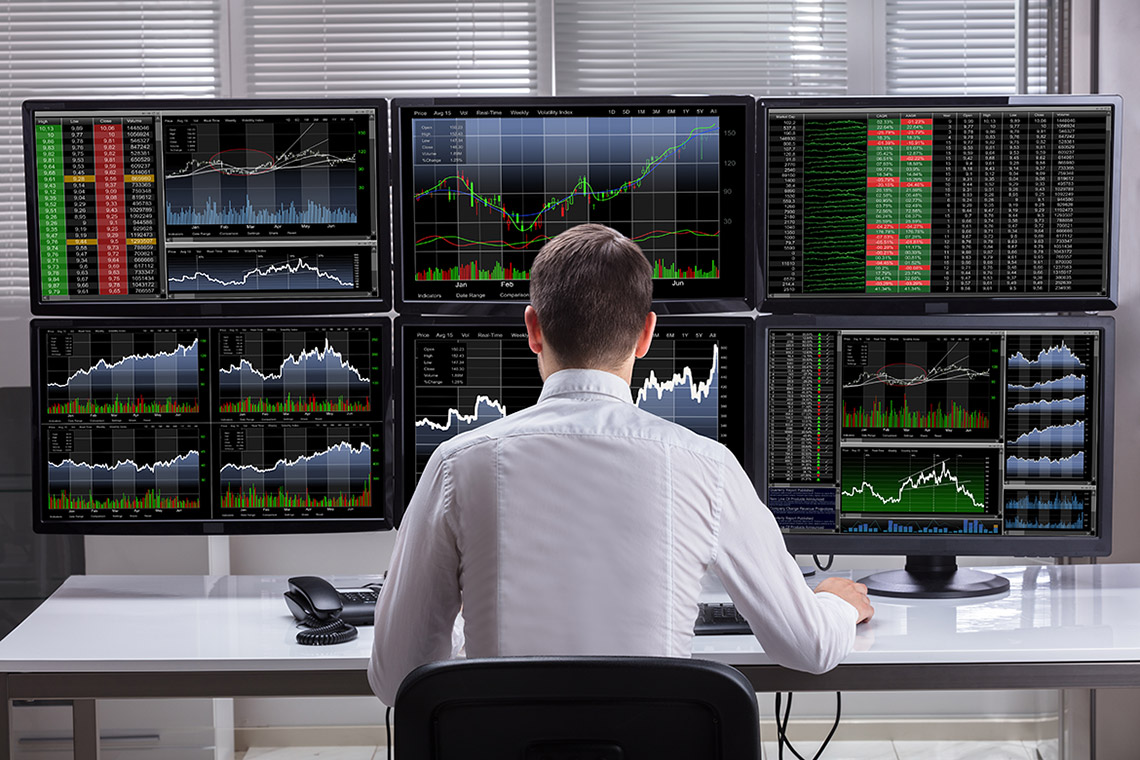
Brian D. Sparling, Senior Member of IEEE, and Regional Manager with Dynamic Ratings Inc.
The challenges facing substation owners and operators for the past years are unrelenting and are summed up in one sentence: “Reduce operating costs, enhance the availability of the generating and transmission equipment, and improve the supply of power and service to the customer base.” All this, in an environment where the available resources are inexorably decreasing and the pressure from the shareholders and the competition mount steadily. Critical oil-filled electrical equipment, such as transformers, shunt reactors, current transformers, circuit breakers and bushings, are key elements of an electrical power system. The reliable and continued performance is the key to profitable generation and transmission of power. The early detection of incipient faults in these assets can create economic benefits that have a measurable impact on the results required to meet these formidable challenges.
Thus continuous on-line monitoring Intelligent Electronic Devices (IEDs) have become commonplace and, with improvements in sensor technology and with built-in intelligence, have demonstrated their ability to meet the challenges. However, there are still some myths and misunderstandings surrounding the application of and benefits to be gained with these devices. These need to be brought out and discussed. During my twenty-plus years in this field, there persist what I call myths surrounding the use and at times misuse of these IEDs. In this article, I will try to bring out the most frequent of these myths.
Myth: If I use these IEDs, it will prevent the failure of my transformer or circuit breaker.
False
The truth is, if a piece of equipment is on its way to a failure, and nothing is in place to advise the owner of its imminent failure, then it will fail. There are of course protection devices (so-called transformer protection relays, etc.) to advise the owner of its failure (or failure to perform its function). These devices do nothing to protect or save the equipment. Their sole purpose is to remove that piece of equipment as quickly as possible from the system to avoid system problems. In other words, they are system protection relays and are not designed to protect the transformer.
A properly selected and applied monitoring IED is there to provide the early warning of a developing fault within the equipment. The warning to the owner is there to initiate some investigation and corrective action. One of the primary reasons for the use of the IED(s) is to reduce the risk of unexpected failure, not to stop a failure from occurring.
Another truth: These IEDs can and do provide early warning of symptoms of a potential defect, but the transformer failed anyway, occasionally catastrophically. This has happened more than once. The primary reason is that the system was not connected to an alarm annunciator, or into an RTU, because the job (installation and commissioning) was, in my words, NOT completed. By NOT completed I mean that no means of communications were connected to (at a minimum) the relay alarm outputs, or via Serial or Ethernet communications networks to some device to pass on the alarms. Speaking of alarms, another failing to complete the job item is training of the operators, or others to be able to respond to the alarm. These systems will deliver “new types” of alarms that some operators have never been trained in, i.e. how to respond to alarms they have not seen before. Some deeper understanding of the alarm and the consequences of ignoring these alarms must be communicated to those who are responsible.
Table 1 presents an example of such an alarm statement, with a recommendation of next steps, to ultimately making an informed decision. These two are only the beginning; a listing of ALL possible alarms needs to be defined and operators trained.
Myth: If I use these IEDs on my equipment, they will advise me of ANY defect or malfunction of that equipment.
False
The truth is, primary equipment has many failure modes and a good many are VISUAL. When performing an FMEA (failure modes and effect analysis), and all possible failure modes are listed, then lined up with technology and/or methods that can be used to detect the symptoms of those failure conditions, I have found that between 30 % and 40 % of failure modes are VISUAL in nature.
Table 1. Example of alarm statements, with recommendations of next steps necessary for making informed decisions
Alarm condition | Diagnostic | Prognostic | Recommendations |
|
|
|
|
| The DGA Monitor HI relay has been triggered because of one of the following:
|
|
|
Small oil leaks (for example) from the tank or bushings cannot be readily detected with any effectiveness by a sensor, other than oil level indicators until it is too late to prevent a forced outage (low oil level), or indeed a failure. Also, oil leaking (or seeping) indicates that the pathway for oil to escape is also the pathway for moisture and oxygen from the ambient air to find their way in. The process of these unwanted elements will not normally cause immediate failure of the equipment, but left alone, with increasing amounts of each accumulating over time, it will accelerate the ageing of the insulation system, thereby potentially shortening the life of the unit. This implies that periodic substation inspections will still be necessary, but perhaps on a reduced frequency.
Myth: I will install one IED system on one unit of two of the same make, and type in the same location. I will then understand how each performs based on the behaviour of one.
False
It would seem logical that two units of the same design, make, vintage and location, exposed to the same loading and environmental conditions, would behave the same. The truth is, every transformer behaves differently once in service. There have been cases where design defects do appear after some years in service, and will ultimately affect the performance of the units. In these cases, monitoring becomes critical. The design issue may be related to some of the common subsystems, such as bushings, or certain vintages of OLTCs. In the case of bushings, there have been cases where design defects begin to reveal themselves after some time in service, but the owner may not have the funds to replace all at the same time. Therefore, they may apply on-line monitoring systems, specific to a vintage of suspect bushings, waiting for the day when it becomes apparent it is on its way to failure. When that happens, the bushing is tested on-site to confirm the alarm and replaced.
“It would seem logical that two transformers of the same design, make, vintage and location, and under the same loading and environmental conditions, would behave the same, but in fact, every unit behaves differently once in service.”
Experience has shown that some bushings with design defects may stay in service longer due to a variety of reasons such as environmental conditions (colder climate), or less thermal stress on the insulation system due to loading conditions. However, it then becomes not a matter of IF it will fail, but a matter of WHEN. Online monitoring of problematic bushings has been done, and once the symptoms of failure begin to reveal themselves, the system alarms, and the response to alarm plan has been carried out, the replacement can be achieved.
Table 2. The questionnaire was taken from the Cigré TB 630
Item number | Issues to be addressed |
1 | Does the company have a clear idea about the type of solution that should be implemented (substation level, enterprise-wide, integrated with SCADA, LAN/WAN, cloud, a few units or fleet-wide, etc.)? |
2 | Is that fully in line with general company strategy (i.e. smart grid initiatives, current trends, change to CBM, postpone investments, increase availability, reduce risks, etc.)? |
3 | Are stakeholders and their roles clearly identified (planning, engineering, maintenance, operations, IT, etc.)? |
4 | Are IEDs, Substation Gateways and Enterprise Gateways in place for the solution? Have eventual changes in databases and IT solutions been properly addressed? |
5 | Have the issues related to communications, protocols, interfacing with existing solutions been sufficiently discussed? |
6 | Is it clear which assets have the highest priorities to receive the new solution (both new transformers and existing transformers)? |
7 | Are the substations prepared for the integration (cables, ditches, communications, etc.)? |
8 | Has the company defined a full strategic implementation, including ownership of the solution, maintenance providers, detailed responsibilities, etc.? |
9 | Has the TICM spec been defined and approved internally (parameters, format, storage, communications, hardware, software, configurations, alarms, messages, etc.)? |
10 | Is it well defined how and by whom each output of the system is going to be used internally? |
11 | Has the company performed a thorough cost-benefit analysis after questions 1-10 that shows adequacy of the chosen solution? |
What can I do? How do I move forward?
The market now offers plenty of sensors, IEDs, on-line continuous monitoring systems, analysis algorithms and software systems for condition evaluation. However, there is no common practice on how to manage the whole process and convert a large amount of data into useful and relevant information. Common ideas and designs would enable the construction of a Transformer Intelligent Condition Monitoring (TICM) System, flexible and extensible enough to meet utility needs now and in the future. Fortunately, much work has been done in the IEEE (transformers committee) world as well as Cigré (A2 Transformers SC) in the past few years, and more is planned, to assist asset managers, maintenance and operations personnel, as well as IT and communication infrastructure people.
The IEEE Guide C57.143-2012, Guide for Application for Monitoring Equipment to Liquid-Immersed Transformers and Components, is available to guide the owners in how to begin to determine the methods, techniques and technologies used to detect symptoms of failure conditions, based on an FMEA. This guide has recently been brought forward for early renewal. Normally, the IEEE Guides and standards have a 10-year life cycle. However, in this case, technology and application of technology and communications have changed rapidly, to the point that much new information is needed.
The Cigré WG A2.44 has produced and now published a Technical Brochure (TB 630), Guide on Transformer Intelligent Condition Monitoring (TICM) Systems, to provide guidance to manufacturers, utilities and other transformer owners interested in understanding the main aspects involved with TICM.
This Guide is designed to define projects, processes and specifications to utilize best practices and maximize the use of condition monitoring (CM) and diagnostic information. It provides guidance to improve asset management techniques with the large-scale (or small-scale) use of integrated information systems and recommends actions for the use of existing online continuous monitoring systems and TICM systems.
One aspect of the Cigré TB 630 provides focus and addresses issues where many initial users of monitoring systems fell down. The Working Group felt that we needed to provide a type of a “checklist” of items that needed to be taken into account and evaluated to provide the owner with some basis of understanding of the requirements needed for a successful implementation.
Table 2 presents the questionnaire taken from the Cigré TB 630. Those asset owners who have taken into account these items have had measurable and positive results. San Diego Gas & Electric has implemented such a largescale system, involving 300 transformers in their transmission and distribution network over the past eight years, and published more than one technical article describing their approach and results.
To date (August 2016) they have achieved the following results:
- Ten transformer failure saves between 15 and 50 years of age 12 capital deferrals
- Life extended from 60 years old to at least 65 years old
Four DGA saves:
- two transmission transformers
- two distribution transformers
- watching other transmission and distribution transformers
- seven bushing saves
The program involves a dedicated team within the utility and the selected vendor where constant improvement is key to continued success. One aspect that has worked was their decision to work with one vendor of the monitoring system, which has demonstrated a continuous support role, involving not only supply but engineering and training assistance.
This aspect has enabled the training of the SDG&E staff to understand and become experts themselves in ONE system that is common across the fleet. They did not have to learn operating procedures on different vendor technologies and software. They established a “lab” where new employees would be trained on the system and try themselves different approaches and analytical models, as they discovered them based on their operating experience. This is particularly true in the case of responses to alarms from bushing monitors applied to different and new component design technologies.
Many of these “findings” and understanding of equipment operation would not have been possible without a dedicated team supporting the system, and certainly without real operating data recording the changing behaviour of their installed fleet.
This article was first published on Transformers Magazine Vol. 4 Issues 2