Should Condition-based Maintenance form part of your maintenance programme?
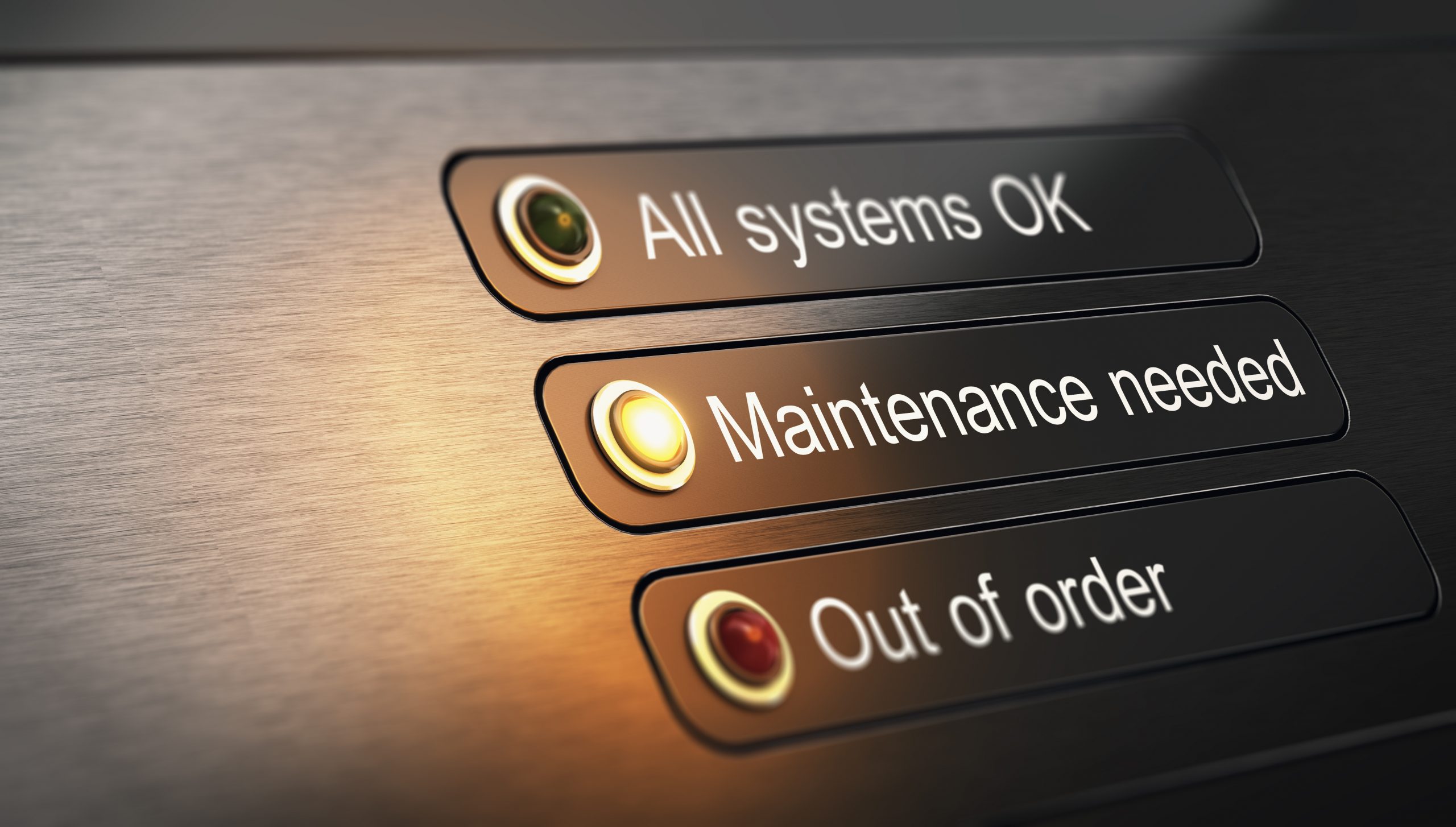
In this day and age, where technology is a great enabler in helping to predict equipment or plant downtime, one would reckon that most asset-intensive companies have condition monitoring as one of the arrows in their tactical maintenance quiver. With condition-based maintenance in place, you get a better understanding of the condition of your equipment which in turn helps you to do the appropriate maintenance when required. The spinoff to this is increased production, improved safety, reduced maintenance costs and failures, a controlled budget and ultimately – longer-lasting assets.
While there is a definite increase in the number of companies using CM technologies and services, we still encounter businesses either with limited /failed or partially implemented CM programmes, or no plan business strategy related to their reliability or condition monitoring programmes. So why then do engineering managers not include condition monitoring in their maintenance and reliability programmes? We’ve found a lack of knowledge and some misconceptions about condition monitoring being the biggest culprits. In this article Gerrit Visagie, Martec Condition Monitoring Consultant will address the issues at hand.
What is condition-based maintenance (CBM)?
Those activities involving continuous or periodic monitoring and diagnosis in order to forecast component degradations so that as-needed, planned maintenance can be performed before equipment failure.
The purpose of CBM as a tactic is to prevent unacceptable consequences by monitoring asset conditions. CBM is predictive in nature with periodic inspections or condition monitoring being carried out to assess the asset condition. If the condition is unacceptable corrective follow-up maintenance is initiated.
CBM is applied when the deterioration in asset health or performance is detectable, or there is adequate warming time to react (PF interval is large enough, HSSE issues are addressed and it is cost-effective).
We suggest two standard tasks to be included in your enterprise asset management system to do inspections and follow-up’s which can be activated based on inspection findings.
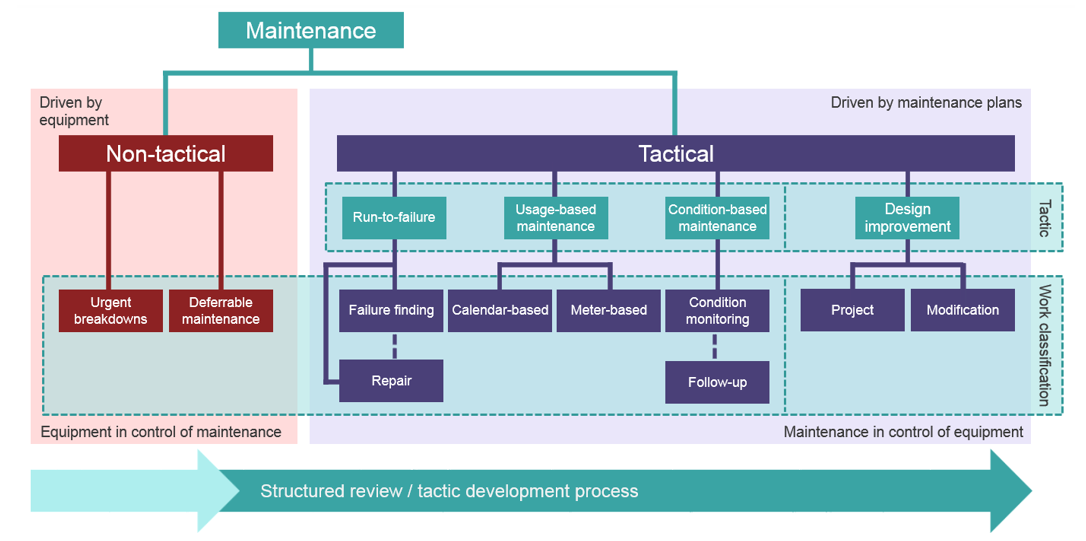
When is condition-based maintenance feasible?
We feel you are doing it right when you get the following results:
- The potential failure mode can be clearly defined and detected.
- The period from detection to failure (P-F) is fairly constant and predictable.
- It is practical to monitor at intervals smaller than the P-F interval.
- The warning level is detected long enough before failure to allow the intervention.
What are some of the most important value-adds of CBM?
- You can plan and schedule corrective action in good time, which include your spare parts, materials and special resources.
- You can conduct appropriate maintenance with the right people and at the right time and place.
- With selected or target maintenance you become more efficient and reduce downtime.
- You can eliminate defects that would result in failures.
- With more control over your budget, you stabilise and then start decreasing maintenance costs.
- Well maintained assets have an increased lifespan.
- By mitigating breakdowns on certain critical assets, you reduce the risk of collateral asset damages.
- Decision making becomes easier with better insights available.
How can we calculate the return on investment when implementing condition monitoring?
This is a very important question as it definitely justifies the investment of implementing condition monitoring, CBM and even something like asset health management.
Here is a simple calculation to determine the return on investment:
- Estimated cost if the asset run to failure = R735 000
- The actual cost of PDMR (eg. Parts, consumable materials, contractor support, repair shop cost, etc) = R 143325
- Cost avoidance for this PDMR = R735 000 – R 143325= R591 825
This is an important cost to consider as part of the overall maintenance budget, especially as input into life cycle costing for specific assets of high value and budgeting purposes.
What are the typical technologies or tactics (approaches) used for mechanical equipment?
- Technologies that are widely used are the following:
- Vibration monitoring/ Portable and permanent monitoring systems
- Ultrasound/ Portable and permanent monitoring systems
- Motor Current Signature Analysis (MCSA)
- Oil Monitoring (Tribology)
- Thermography (IR Imaging)
- NDT (Non-destructive testing)
What steps should be taken to compile an integrated CBM and asset management plan?
Again, one needs to define the goal and endpoint of what you want to achieve.
|
From my experience and perspective, I would suggest the following steps:
Step 1 | Identify the assets that you want to monitor. Concentrate on assets that are:
- Criticality – Importance to production and organisational success
- Costly to repair and replace
- Not going to be replaced any time soon
- Reaching the end of life
- High Failure rate
- Long replacement lead time
Step 2 | Identify all known and probable failure modes
- The best way to do this is by performing an RCM analysis and focus on the failure modes that can be managed using CBM strategies.
Step 3 | Select the right CBM solutions and monitoring techniques
- A condition monitoring technologies road map can help prioritise what to get and can allow for a gradual uptake to assist in change management when implementing new tactics.
- Choose the correct CBM technology based on the FMEA/RCM Analysis for the specific assets
Step 4 | Define baseline limits for chosen CBM solutions
- You need to define acceptable condition limits so that the system can warn you when monitored equipment is starting to deteriorate. These limits have to be set in a way that you have enough time to perform corrective actions.
Step 5 | Establish the CBM program
- Running any maintenance program requires you to define tasks and responsibilities and assign them to your maintenance team. Collecting and recording measurements should be in the centre of your plan.
Step 6 | Analyse the data and act accordingly
- Analyse the data coming in from sensors and inspections to plot a trend and schedule maintenance work accordingly.
Who oversees this plan?
Ideally, this would be the responsibility of the reliability engineer, manager or technician. It also depends on the availability of competent persons. I have come across many plants with a condition monitoring technician leading the team.
How do CBM and normal scheduled maintenance fit together?
Both are maintenance tactics and they should form part of the same asset management strategy. The structure of the asset management department will determine how these activities are executed, but in general, the person responsible for CBM, usually a reliability engineer, will identify and report the defects and recommendations to the planning department which will, in turn, instruct the maintenance department to go and do the corrective actions. We have encountered tension between the various departments as CM is sometimes perceived as a ‘policing tool’ as it can highlight the absence of maintenance and imply that the maintenance team did not do their work. Companies must invest in training people to understand the value and place of condition monitoring and how it supports their collective efforts to improve the performance of their equipment.
Historically most plants had their own condition monitoring departments, but as with many other special functions, more and more companies tend to outsource this function to a specialist condition monitoring company. In my view, this service provider should become an extension of the asset management team and work towards the same goals as stated in the strategy.
What are the typical misconceptions about condition monitoring?
- Condition monitoring is expensive – Equipment can be expensive, but part of the strategy can be to appoint a condition monitoring partner to do the work for you. This reduces the need for upfront equipment costs.
- Condition monitoring is time consuming and a complex task – With the right equipment and experience you can quickly and effectively set up equipment in the database (or on the datalogger itself) and take multiple data points in a matter of minutes.
- Specialists must gather and analyse data – With some very basic training, a lowered skilled person can gather the correct information and send it to an adequately skilled person or CM partner to analyse, interpret and advise on what to do.
- Each and every piece of equipment must immediately be included in the CBM programme – Start with a pilot plant and equipment and gradually include more assets from thereon.
To find out how CM has helped companies, you can visit the Martec resource page to browse through our case studies and client reference stories. You can also read our value-adding TechTalks that unpack the different condition monitoring applications and tactics.